Table Of Content
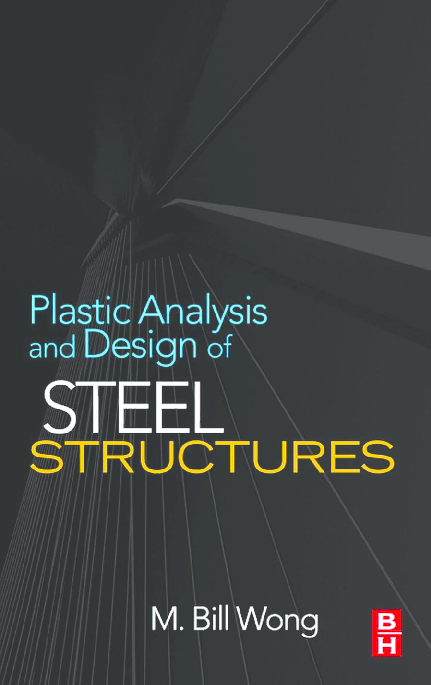
Polycarbonate sheets are popular among architects and interiors designers for their ability to maximise natural light while maintaining privacy, as well as improving a building's thermal insulation. However, with growing efforts to decarbonise the economy, non-fossil alternatives are being developed in a bid to meet the ever-increasing demand for plastics in a more sustainable way.
Barn-like house
With cutting-edge technology and a skilled team of professionals, we turn concepts into reality, delivering high-quality custom products tailored to your exact specifications. How features of a part are formed during a mold determines the type of draft needed. Most bosses, ribs, and posts formed by blind holes or pockets should taper thinner as they extend into the mould.
Elegance. Style. Quality.
For eg, for injection molding, it is advised to keep a Uniform Wall thickness within a range of 1.5mm - 3 mm. Once discarded, designers have been able to repurpose this packaging into sculptural chairs and beckoning cats, as well as melting it to create moulds. In architecture, it can be used for insulation or more experimental applications as in ADX's Soil House (above), which features walls of loose soil fixed in place with a foam spray. IDS always designs every product to comply with manufacturing practices that match your vendor’s capabilities.
Our Most Popular Service Areas:
Molded-in snap locks enable designers to assemble parts without additional hardware. Although snap fits must be correctly designed for reliable performance, they are highly beneficial to the end-user and the manufacturer. And this starts with how we design products and packaging material in the goods we manufacture and deliver. We need responsible design and production solutions that facilitate a product and package redesign that enables companies to engage in the circular economy and reduces waste without sacrificing quality.

With guests Rosalie McMillan, Co-founder of Smile Plastics, and Daniella Souza Miranda, Global Marketing Director at Dow, we explore how large and small businesses are implementing design thinking into their core strategies. Together with our in house tooling department, Design Plastics's Engineering department can assist our customers with all their design needs from start to finish. This month's Dezeen In Depth newsletter delves into the debate surrounding the future of plastics and features an exclusive interview with interior designer Kelly Wearstler. From concept to creation, our streamlined process ensures efficiency and top-notch results, making us the preferred choice for businesses seeking excellence in custom plastic solutions. Design for assembly (DFA) is a process that ensures ease of assembly in mind with the final goal of reducing assembly time and cost. The reduction of the number of parts of an assembly is usually where the major cost benefits of DFA occur.
Plastics materials Selection for Injection Molding
TrinamiX enables flexible identification of plastics and textiles at the push of a button. In addition, textiles that are made from more than one material can also be identified. With over 25 years of industry-specific experience in thermoformed food packaging, Colin Winkler has a true passion and love for plastic thermoforming and strives to continue the legacy his family has built within the plastics industry. When he’s not busy helping clients or running the company, Colin enjoys spending time with his wife and two daughters and pursues a hobby of collecting and working on cars.
Ask about our prototyping and samples for your project so you can see your items before a production run. The API engineers and designers have over 250 years of combined experience and strive to exceed our customer's expectations. Bosses can be added to the part design for assembly, locating, or mounting of a part.
As a result, this year’s Earth Day theme— “Planet vs. Plastic”— demands a 60% reduction in the production of all plastics by 2040. A diverse digital database that acts as a valuable guide in gaining insight and information about a product directly from the manufacturer, and serves as a rich reference point in developing a project or scheme. Both the contact molding and filament winding techniques are used to create tanks.
The Dezeen guide to carbon
Translucent Plastics Deliver More Automotive Design Freedom - PlasticsToday
Translucent Plastics Deliver More Automotive Design Freedom.
Posted: Wed, 29 Nov 2023 11:41:39 GMT [source]
Design for Manufacturing (DFM) elaborates the process of designing a product to reduce its manufacturing cost, allowing problems to be sorted during the design phase itself which is the least expensive phase to address. To avoid thick sections, uniform wall thickness throughout a part (if possible) is essential. Sent every Thursday and featuring a selection of the best reader comments and most talked-about stories. This includes recycled plastic, which presents a huge source of untapped potential as only nine per cent of the 8.3 billion tonnes of plastic waste produced across the world have so far been turned into new products.
But when incinerated, as 12 per cent of all plastic waste is, this carbon is emitted as carbon dioxide. This helps to make plastics more affordable than most other materials and sees them used to create millions of tonnes of single-use items every year. They can be divided into thermosetting plastics, which never soften once moulded, and thermoplastics, which can be melted and reshaped, making them more suited to recycling. Along with our distribution and in-house fabrication, Design Plastics offers on-site repairs, field service and fabrication from both locations. You can also go to earthday.org to learn more about the battle between planet vs. plastics, and find an event near you where you can help clean up the planet. Think about optimizing your entire supply chain for sustainability, rather than just individual functions.
Improper placement of a boss leads to uneven wall thickness and can have a negative impact on the aesthetics, shrinking, or strength of a part. Thin gauge thermoforming consists of plastic sheeting that is between .010" and .040" and usually comes on a roll and gets fed through the thermoforming machine on pins or spikes. The products made from thin gauge plastic are primarily used for things like clam shells, blister packs, disposable cups, food containers, plastic lids. As an alternative to cutting and assembling plastic, vacuum forming allows parts to be formed as a solid piece without seams. Dekker Design can produce all necessary molds to vacuum from plastic to customer specifications. Many people think that by making the walls of an element thicker, the strength of the part will increase.
The increasing complexity of plastic injection moulded parts is another reason to choose a moulder who follows DFM principles. To meet the quality/cost requirements of customers, tolerance, draft angles, undercuts, and other factors must be considered during the design stage. Industrial designers are continually challenged with preserving their concept design intent as it is transformed into a production design. This delicate process can be managed efficiently if the industrial design firm is knowledgeable about mold design and the specific plastic molding process. IDS has a comprehensive understanding of mold design and routinely translates its highly innovative designs into practical, easily molded plastic parts.
Consideration of those elements is prime for integrating engineering and manufacturing expertise to catch mistakes, see opportunities for efficiencies and price reduction, and even assess the viability of contract requirements. Typically, your injection molder will conduct an in-depth analysis of those elements together with your team well before the tooling process is initiated. DFM isn't a “stand-alone” guideline or principle when it involves manufacturing plastic injection molded products. It works with other approaches for optimization of design like designing for functionality, assembly, and sustainability, each of which is discussed further, below.
As Earthday.org says, “We need to invest in innovative technologies and materials to build a plastic-free world”. A Life Cycle Assessment is a method for the compilation and evaluation of the inputs, outputs and the potential environmental impacts of a product throughout its life cycle (ISO standard 14040). Our entire operations are located in Los Angeles just minutes from LAX, which means our custom containers are 100% made in the USA. We also offer convenient shipping all over North America, without the lengthy delivery times typical of overseas manufacturers. We specialize in the design and manufacture of quality plastic parts for worldwide industry. With our skills and an earned reputation for excellence, we can create the ideal promotional materials for any brand.
No comments:
Post a Comment